Silica sol precision casting |
 |
|
Publisher: Wuxi Yongsheng Metals Goods Co.,Ltd. Release Time:2016/10/24 10:33:56 Clicks:1933
Close |
|
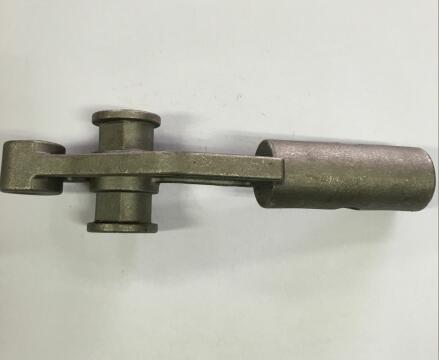 |
|
Product Details
|
In the production of stainless steel products, some products, the shape of strange, can not use the process of production such as bending, for the production of such irregular shape (internal or solid) products, the use of wax mold → do sand mold → Liquid material filling molding process. Advantages: can be made according to different wax patterns of changing products. Disadvantages: forming blank accuracy is not high, the surface roughness. Second, the casting process 1, according to different shapes of products do die. Die points up and down mode, through the car, planing, milling, erosion, EDM and so on Integrated process is complete. Dent shape, the size of the same product with half. Because the wax mold is mainly used for industrial wax pressure type, so the selection of the melting point is not high, hardness is not high, lower requirements, the price is cheaper, lighter weight aluminum alloy mold. 2, the use of aluminum alloy die to produce a large number of industrial wax solid model. Under normal circumstances, an industrial wax solid model can only be Corresponding to a rough product. 3, the margin of the wax mold to carry out intensive, deburring after a number of single wax mold stick (also known as the group tree) prepared in advance Die head, the die is also used to produce the wax model of industrial wax solid model. (Shape much like a tree) 4, will have been fixed in the die on a number of wax coated with industrial glue evenly sprayed with the first layer of fine sand (a refractory sand, high resistance Temperature, usually with silica sand). The sand particles are small and very fine, which ensures that the final rough surface is as smooth as possible. 5, at the set room temperature (or constant temperature) to spray the first layer of fine sand wax natural drying, but can not affect the internal wax mold shape change, the natural air-dry time depends on the complexity of the product itself, the general fine Casting for the first time in about 5-8 hours of air-dried. 6, after the first sand spray and natural air-dried, the wax on the surface of the industrial glue to continue (silicon slurry), and spray the second layer Sand, the second layer of sand particles than the size of the first layer of sand to the large, to the rough. After spraying the second layer of sand is also set in the constant temperature to wax natural dry. 7, after the second sand and natural air-dried, followed by the third sandblasting, the fourth blasting, the fifth blasting and other work sequence. Requirements: - According to the product surface requirements, size, weight and so adjust the number of blasting. Under normal circumstances, the number of sandblasting for 3-7 times. - Each time sandblasting the size of the sand are not the same, usually after the process of sand than the previous process of coarse sand, air-dried time is not the same. Generally a complete wax on the sand production cycle of 3 to 4 days. 8, the sandblasting process has been completed in the baking process before the wax model, and then evenly coated with a layer of white industrial latex (silica sol), in order to play a bonding and curing sand, and sealing wax model role for the post Road baking process to prepare. At the same time in the baking process, but also improve the brittleness of sand, easy to crack the sand layer, remove the rough. 9, baking process Will be fixed in the die, and complete the sandblasting drying process of wax into a special sealed metal oven heating (commonly used is Burning kerosene steam furnace). Because the melting point of industrial wax is not high, the temperature is about 150 ゜ or so, the wax mold heat melted to form wax water along the gate outflow, this process is dewaxing. Wax from the end of the wax is just an empty shell. The key to precision casting is to use this empty sand shell. (Normally this wax can be used repeatedly, but these waxes must be re-filtered, otherwise the wax will affect the rough surface quality, such as: surface sand holes, pitting, but also affect the shrinkage of the casting products). 10, baking sand shell In order to make the finished wax shell more solid and solid, before pouring stainless steel water, must be baked sand shell, usually at temperature Very high (temperature about 1000 ゜ or so) stove baking. 11, will have high temperature dissolved in liquid stainless steel water into the finished wax shell, liquid stainless steel water is filled before the wax Mold forming space until fully filled, including the middle of the die part. 12, because the stainless steel boiler will have different ingredients mixed with the material, the factory must test the material percentage. Then according to The required proportion of the release, for example, to increase those aspects of the elements, to achieve the desired effect. 13, liquid stainless steel water cooling after solidification, by means of mechanical tools or manpower will be the outermost layer of sand crushing, exposing solid Of the stainless steel product is the original wax shape, that is, the final blank required. And then one by one cutting, separation and then by the coarse grinding to become a single blank pieces 14, test rough: the surface of trachoma, stomata of the blank must be used argon arc welding, serious when the waste cleaning and re-furnace. 15, cleaning blanks: After passing the blank must pass the cleaning process. 16, for other processing processes, until the finished product. |
About Us
|
Wuxi Yongsheng Metals Goods Co.,Ltd.
Hotline:86-13806173867
Contact: Zhiyong Lu
Contact: Miss Ma
Tel: 0510-68916532
Fax: 0510-68916533
E-mail: lyzz@vip.163.com
caochuantou@163.com
Website:http://vistasp2.cn
Address: No. 38 Xiqun Road Industrial Park, Jiangsu Wuxi Meicun
|
Order online
|
|
Related Products
|
|
|